Ready-mix c (RMC) is a pre-mixed form of concrete that is manufactured in a factory or batching plant based on a specific recipe, which is then delivered to a construction site via truck-mounted transit mixers. This type of concrete offers a precise mixture, allowing for the creation of specialised concrete blends to be used in construction projects.
The first factory specifically designed for the production of ready-mix concrete was established in the 1930s. It wasn’t until the late 1980s that the industry began to expand rapidly.
RMC is often preferred over on-site concrete mixing for its ability to produce large volumes with a high degree of precision in the proportion of ingredients used. However, it is important to note that ready-mix concrete does come with certain limitations.
Graana.com has gathered information on ready-mix concrete, along with its types and advantages, and disadvantages.
Types of Ready-Mix Concrete
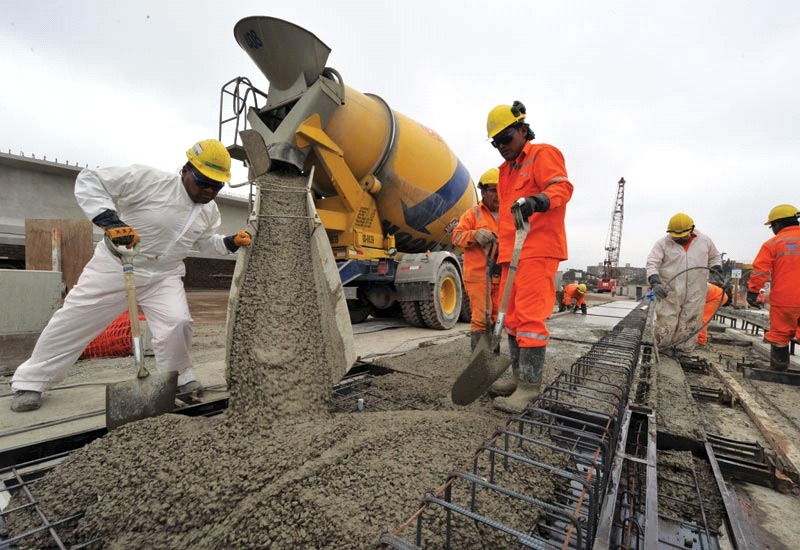
There are three types of ready-mix concrete (RMC) depending upon the mixing of the various ingredients as given below:
Transit mixed concrete
Transit mixed concrete, also known as dry-batched concrete, is a type of ready-mix concrete where all the ingredients are loaded directly into the truck mixer. The mixer drum is then rotated at a high speed during the loading process and at a slower agitating speed during transportation to the construction site. There are three variations of transit mixed concrete:
- Concrete is mixed at the job site, where the drum is rotated at a high speed just before discharging the material to ensure homogeneous mixing.
- Concrete mixed in transit, where the drum speed is kept medium during transportation for a certain number of revolutions to ensure proper mixing.
- Concrete is mixed in the yard, where the drum is rotated at high speed in the batching plant before transportation to the site.
Shrink-mixed concrete
Another type of mixed concrete is shrink-mixed concrete. It is ready-mix concrete where the mixing process is partially done at the central batching plant.
It is completed during transportation using a truck-mounted drum mixer. The extent of mixing at the central plant is determined through tests to establish the requirement for mixing in the drum mixer.
Central-mixed concrete
Also known as central batching plant or wet-batch concrete, central-mixed concrete is a type of ready-mix concrete. The ingredients are thoroughly mixed before being loaded into truck mixers. During transportation, the truck mixer acts as an agitator only. In cases where low workability or short lead time is required, non-agitating units or dump trucks can also be used.
Each of these types has its own advantages and disadvantages. The most appropriate type will depend on the specific requirements of the project.
Central-mixed concrete is ideal for large-scale projects where consistency and high-quality concrete are required. While transit-mixed concrete is more suitable for smaller projects with a quick turnaround time. On the other hand, offers greater control over the mixed design and quality control at the construction site.
Process of Ready-mix concrete
Ready-mix concrete is a pre-mixed form of concrete that is made with a combination of cement, aggregates, sand, water, and other chemicals that are weigh-batched at a central plant for optimal quality. The concrete is then delivered to construction sites via transit mixers and can be used immediately without additional treatment.
The automatic plant equipment is used to monitor the weigh-batching, water-cement ratio, the dosage of admixture, and moisture content with precision, to produce high-quality concrete.
Before being used in the production of ready-mix concrete, all ingredients are thoroughly tested for quality and physical properties in a well-equipped laboratory attached to the plant. This ensures conformity to relevant international standard codes.
The laboratory also uses a moisture probe to determine the water content in the sand and aggregates, which helps to determine the proportion of water to be added to the mix. To ensure the quality and consistency of each batch, trial mixes are carried out and tested in the laboratory. This ensures that each batch of concrete meets the specific mix designs as per the client’s requirements and different grades of concrete.
Advantages of Ready-Mix Concrete
The following are the advantages of ready-mix concrete:
Consistency
Ready-mix concrete is manufactured in a factory or batching plant according to a set recipe, ensuring that the concrete is of consistent quality and strength. This eliminates the need for on-site mixing, which can be inconsistent and of lower quality.
Time-saving
Ready-mix concrete plants employ mechanised operations to achieve efficiency and speed in the construction process. The production output from a traditional site-mix concrete plant using an 8/12 mixer is limited to 4 to 5 cubic metres per hour. hereas a ready-mix concrete plant can produce 30 to 60 cubic metres per hour.
Cost-effective
This concrete is more cost-effective than on-site mixing, as it reduces labour and material costs. It improves the efficiency of the construction process.
Additionally, ready-mix concrete eliminates the need for on-site mixing equipment, reducing the cost of investment and maintenance. It also reduces the need for a skilled labour force for mixing and transporting the concrete which can be significant cost savings in certain situations.
Variety Ready-mix concrete
When it comes to choosing ready-mix concrete, it comes in a variety of types. These types include transit mixed concrete, shrinks mixed concrete, and central mixed concrete allowing for the selection of the most appropriate type for a specific construction project.
Quality
A ready-mix concrete plant ensures the production of high-quality concrete by utilising advanced equipment and standardised procedures. The materials, process parameters, and key practices are strictly controlled. This ensures that the problems of poor material control, inconsistent batching and mixing methods that are often encountered in traditional site mix concrete.
Ready-mix concrete is manufactured under controlled conditions, ensuring that the concrete is of high quality and strength. This is particularly important for large-scale construction projects, where the quality and stability of the concrete are critical to the integrity and safety of the finished structure.
Easy to Produce
Creating concrete on a construction site can be a daunting task. It involves the management, storage, and organisation of all the necessary components such as cement, sand, gravel, and other materials. Additionally, it requires a steady source of clean water for mixing the concrete.
It offers a more efficient and effective alternative to these challenges. It eliminates the need for managing, storing, and organising supplies and can be delivered to the construction site promptly, maintaining the continuity of the construction work.
Disadvantages of ready-mix concrete
The following are some disadvantages of ready-mixed concrete:
Timing and Distance
Ready-mix concrete is where the materials are batched at a central plant, and the mixing begins at that very plant. This means that travelling from the plant to the site is critical, particularly over longer distances. If the site is too far away, the ready-mix concrete may become unusable by the time it gets there.
Traffic
Another disadvantage of ready-mix concrete is that it generates additional road traffic. Ready-mix trucks are large in size and may cover many areas on the road, blocking other traffic. Additionally, access roads and site access have to be able to carry the greater weight of the ready-mix truck plus load. This problem can be overcome by utilising so-called ‘mini mix’ companies.
Limited Time Span
The limited time span between mixing and curing means that ready-mix should be placed within 210 minutes. Modern admixtures can modify that time span precisely. The amount and type of admixture added to the mix are very important.
Conclusion
Ready-mix concrete is a convenient and efficient solution for large-scale construction projects. It is manufactured in a factory or batching plant according to a set recipe, ensuring consistent quality and strength. It is delivered to the construction site by truck-mounted transit mixers, reducing labour and material costs.
Visit Graana blog for more related information.